Continuous Optical Bioprinting Brings Unmatched Speed to 3D Cell Culturing and Tissue Engineering
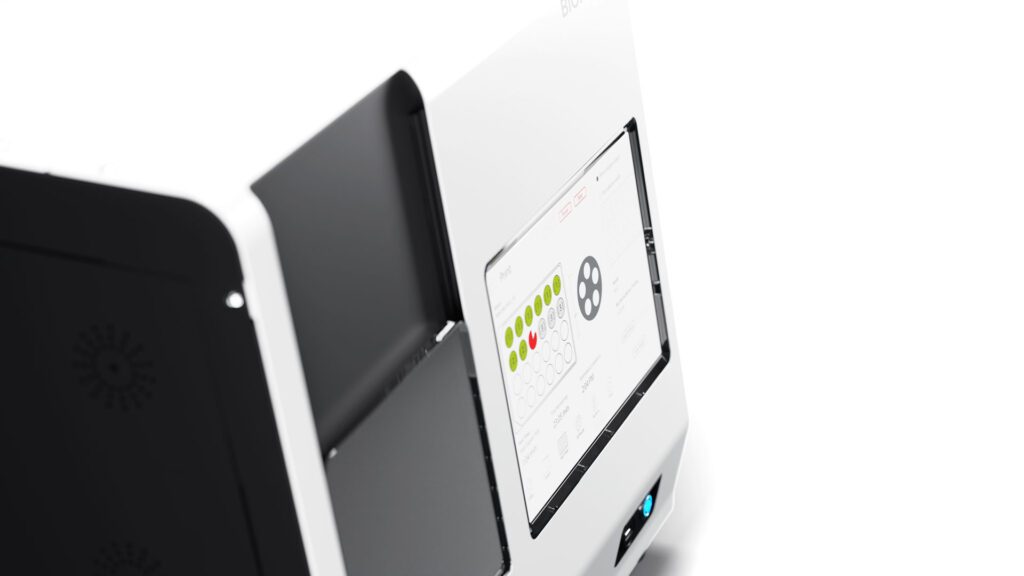
The BIONOVA X is the world’s first digital light processing (DLP) 3D bioprinter compatible with such a wide range of biomaterials and living cells. With this benchtop bioprinter, biofabrication occurs directly in standardized microwell plates, in 6-, 12- or 24-well formats. The standardized microwell plates also boast a glass bottom for seamless integration with downstream processes, like high-throughput live cell imaging and automated liquid dispensing. The BIONOVA X is the product of converging advances in biology, biochemistry, material science and software engineering. It represents a benchmark to measure all future bioconvergence breakthroughs against. Given the unparalleled resolution of its patented microscale continuous optical printing and its compatibility with a wider range of biomaterials and cells, the BIONOVA X increases efficiency in applications such as 3D cell culture, tissue engineering, disease modeling and drug development. This novel DLP bioprinter may even engender previously unimaginable applications.
How does the BIONOVA X work?
Individually adjustable digital micromirrors optically project photomasks onto photosensitive prepolymerized solutions in each well by way of a submergible probe. Simultaneously, a 3-axis motorized stage controls the plate’s movements. This synchronizing of light source activation, photomask pattern sequences and movement of the motorized stage enables the BIONOVA X’s rapid, continuous bioprinting. This novel DLP bioprinter drastically reduces biofabrication time compared to extrusion-based bioprinters.
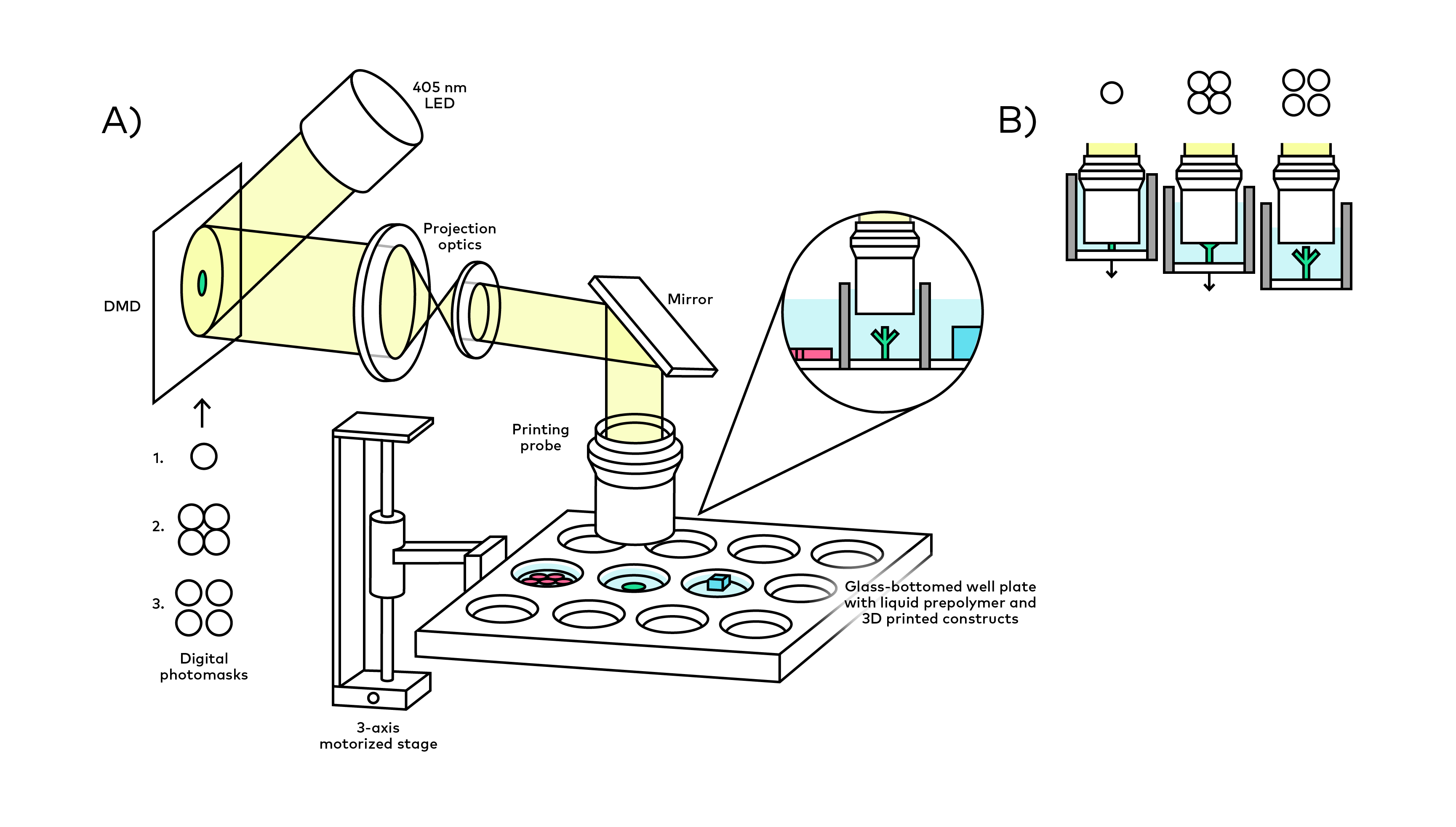
Figure 1. A) Schematic of the BIONOVA X bioprinter, which enables direct in-well printing into standardized multiwell plates. B) Time-lapse depiction of the rapid continuous optical bioprinting of a branched tube construct with the BIONOVA X.
Data-backed evidence
Check out the result from an internal study detailing how the BIONOVA X precisely bioprinted 3D micropillar arrays, which were seeded with stem cells and successfully matured into cardiac tissue. The direct in-well printing of the micropillars also enabled real-time visualization and contactless measurement of the cardiac force with a conventional microscope. Additionally, without removing the bioprinted models from their wells, researchers seamlessly integrated a characterization workflow thanks to the bioprinter’s glass-bottom microwell plates. The plates’ standard sizing means they are easily transferable to other automated instruments, such as automated liquid handlers and live cell imaging systems.
Beyond its unmatched speed, high precision and cell viability, the BIONOVA X introduces new possibilities, such as tunable mechanical properties within the same construct. This fine-tuning is achieved by adjusting crosslinking density with high fidelity and micron-level precision. Check out the research data from our second internal study with the BIONOVA X, which validates the reproducible accuracy of its bioprinting.
DLP bioprinting just got faster
Patented continuous optical printing technology delivers speeds never seen in DLP bioprinting. For example, in one internal study, the BIONOVA X produced 8 micropillar pairs ranging in size from 60 x 135 microns to 135 x 135 microns in a 24-well plate. The continuous optical bioprinting took less than 20 minutes to produce 192 identical pairs of micropillars, exponentially dwarfing the throughput of conventional biofabrication methods.
Have questions?
Don’t hesitate to reach out to our team to learn how the BIONOVA X can be used in your research. Contact us.
Reliable reproducibility
When your drug assay calls for hundreds of functionally identical tissue models, self-assembling co-cultured cells that form spheroids won’t make the grade. The obvious drawback being that self-assembled structures vary too much from one spheroid to another. On the other hand, the automated BIONOVA X uses a motor-driven stage to move along 3 axes. It offers unmatched flexibility that results in 10-micron precision along the X and Y axes and down to 4 μm precision along the Z axis. This precision yields biofabricated tissue scaffolds that are consistently reproducible and could potentially accelerate pharmacological discovery, disease modeling and personalized efficacy drug testing.
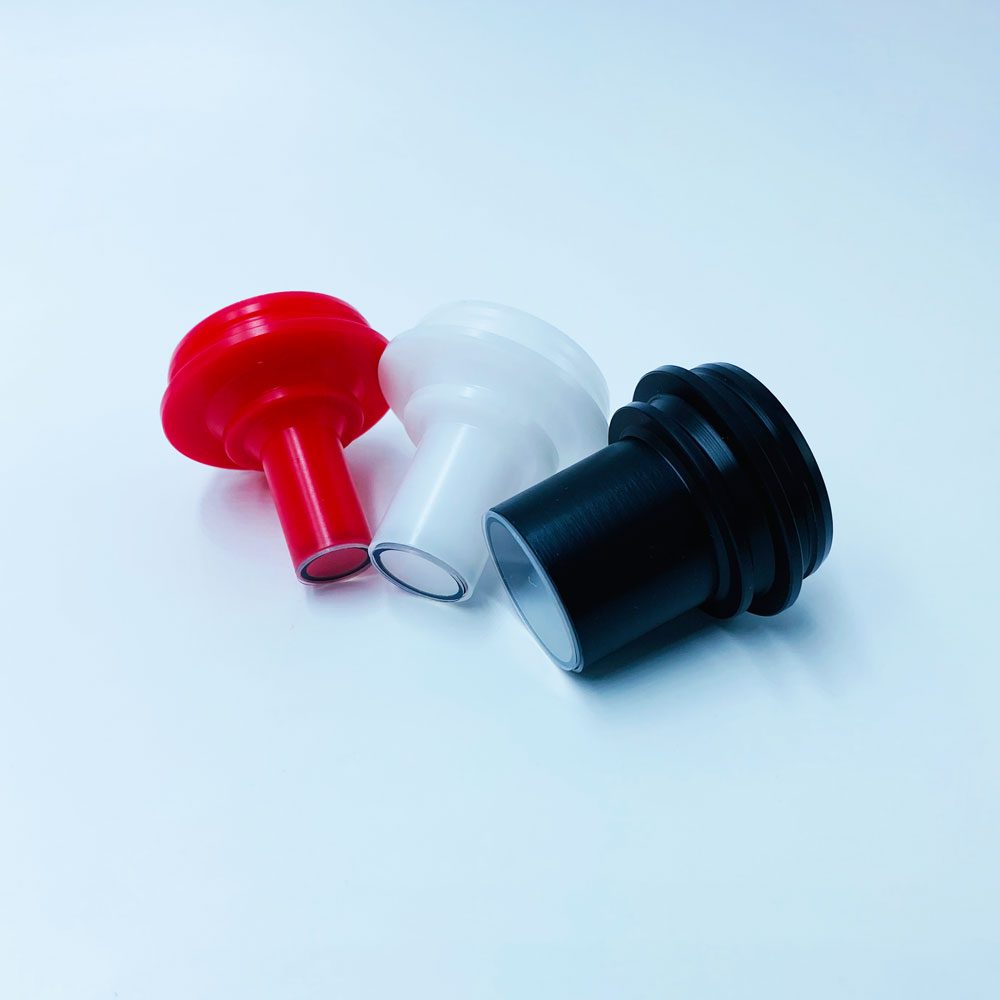
Tunable mechanical properties
The BIONOVA X’s hollow probes boast the unique ability to control crosslinking density, enabling the fine-tuning of mechanical properties within the same scaffold. In other words, its grayscale printing feature allows for the spatial control of light exposure in different regions. Why should researchers care about the precision of gradients? Consider that in an internal study documenting the bioprinting of biomimetic liver models, our application scientists found a positive linear relationship between exposure time and stiffness of a given region. With this novel DLP bioprinter, researchers can pick and choose or mix and match print parameters so that the final polymerized bioconstruct mirrors the variation in stiffness seen in native tissue. They can also reproduce these gradients consistently across multiple constructs to run assays under in vivo conditions in high throughput.
DLP bioprinting with a wider range of biomaterials and cells
While some DLP 3D printing technologies require using proprietary inks or are not cell-friendly, the BIONOVA X is shifting that paradigm. Thanks to its universal bioprinting platform, researchers can use their own photocurable hydrogel-based bioinks. They can also incorporate non-photocrosslinkable biomaterials, like cells, collagen, decellularized ECM and growth factors. One can mix these non-photocrosslinkable materials with carrier components like the ones available in our recently expanded library of photocurable hydrogels. This expanded portfolio includes new formulations with base materials such as PEGDA, alginate, hyaluronic acid and gelatin. During bioprinting, the non-photocrosslinkable materials are trapped in the polymeric network formed when the photocrosslinkable materials are photopolymerized by the BIONOVA X’s 405 nm light emitting diode (LED).
For those looking to develop their own photocurable bioinks, Advanced BioMatrix, another BICO company, offers an extensive portfolio of base materials that can be reconstituted.
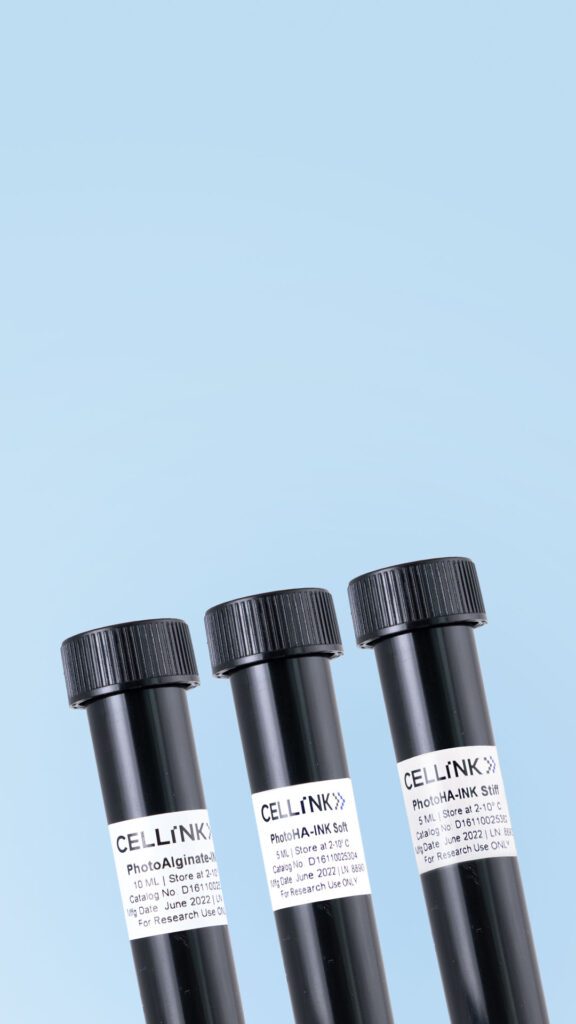
Cell-friendly environment
Beyond mixing living cells with photopolymerizable hydrogels in DLP bioprinting runs, the BIONOVA X boasts additional features that maximize cell viability. First, the BIONOVA X uses cell-friendly light exposure in the form of 405 nm light emitting diode (LED). Two, adjustable temperatures ensure the best conditions for many cell types. Lastly, high-speed continuous optical printing significantly reduces the time cells spend outside the incubator. Put it this way, depending on the complexity of the construct, researchers can bioprint a 24-well plate in under 20 minutes as we demonstrated in this internal study.
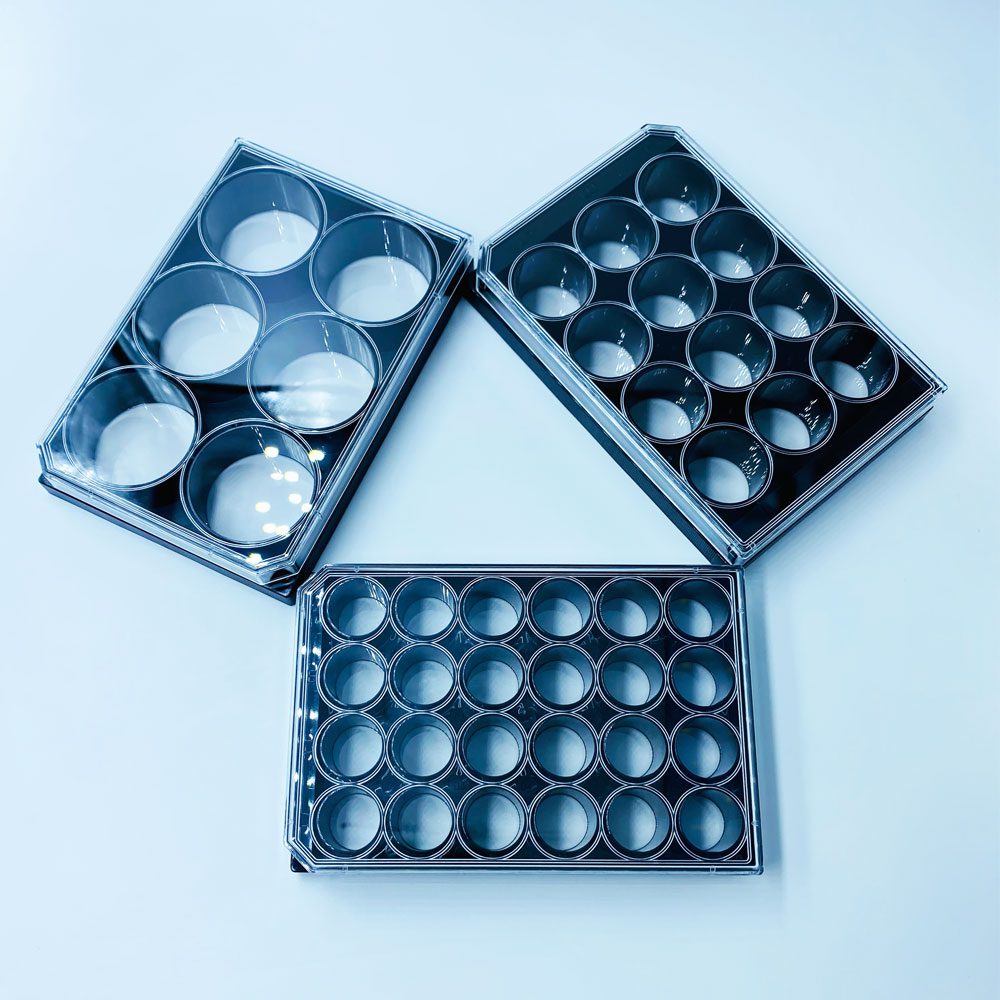
Unmatched sterilization guaranteed
Rest assured, the BIONOVA X’s compact size and specialty consumables simplify maintaining a sterile environment. The bioprinter easily fits inside most laboratory biosafety cabinet setups. Exact dimensions are 20.3 x 15 x 17.4 inches, and the benchtop instrument only weighs 90 pounds, or less than 41 kilograms. Additionally, the specialty probe arrives in sterile packaging and can be used for up to 24 hours of continuous printing. Other consumables, like the standard-size glass bottom microwell plates are available in 6-, 12- and 24-well formats.
BIONOVA X offers A to Z workflow automation
Earlier generations of DLP bioprinters could only produce bioconstructs in single vats. The BIONOVA X avoids the need to transfer constructs manually, which can lead to human error, damage to cells or impede scaling up for high-throughput screening. Because it prints directly in standardized microwell plates, there is no need to manually transfer bioprinted samples for characterization workflows. Long-term cell culturing in incubators, as well as live cell imaging, can happen in the same plate. Plates are also easily transferable to other automated instruments, such as DISPENDIX’s I.DOT liquid handler and CYTENA’s CELLCYTE X imaging system. Lastly, plates are available in adhesive or non-adhesive formats. Bioprinted constructs are either crosslinked to the bottom of adhesive plates or can be easily removed from non-adhesive plates.